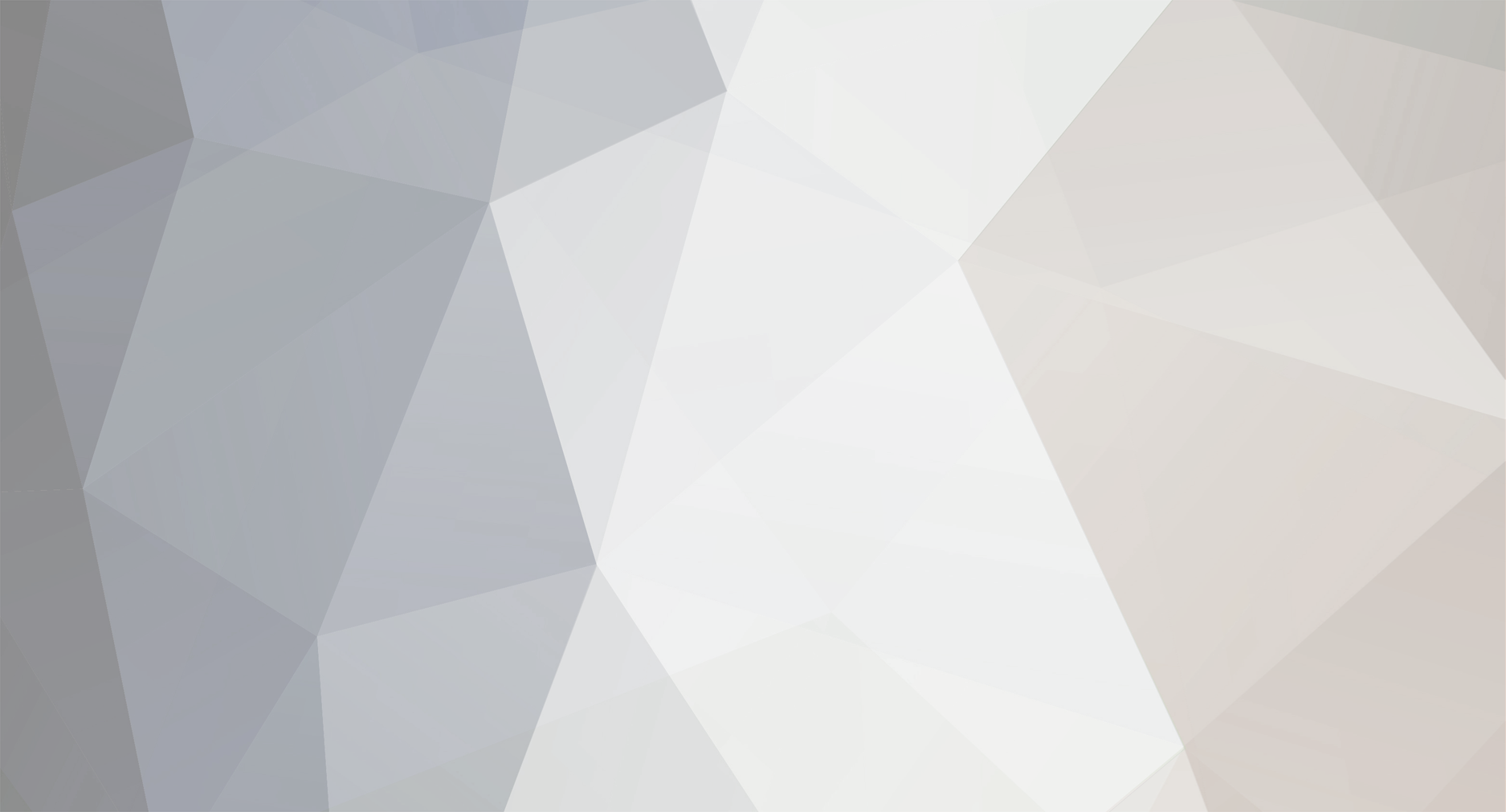
Aburek
Member-
Posts
35 -
Joined
-
Last visited
-
Days Won
1
Content Type
Profiles
Forums
Downloads
Everything posted by Aburek
-
the PFD in the A300/310 does not have an altitude tape.
-
Hi All, Did this not make the SU12 update? Its a fairly large missing bit of info in the FMS. Thanks
-
Can you show the FMS screenshot of the F-PLN page?
-
It is possible to deploy one at a time on the real aircraft. In the case of one reverser being deferred is an example.
-
It should also be noted that the wheel should not spin without G and Y hydraulics pressurized and the pitch trim levers engaged.
-
Its in the settings menu of the EFB.
-
Is nosewheel steering active in the EFB?
-
I believe he means transition altitude/level. As this aircraft is older tech, that is manually set to or from STD by the crew. Theres no FMC setting for that.
-
I believe this is an MSFS code issue. If used with vPilot and VATSIM the TFR switch works correctly.
-
Not seeing this with vPilot.
-
Its consistent. I arm P.DES between 20-30nm prior to T/D, although ive done it earlier just to see if it makes a difference. I believe it is related to any STAR that has a 280KT constraint. It seems the aircraft will speed up to that prior to T/D when in actuality it should descend at the selected mach number and hold at the speed constraint once it reaches it in the descent.
-
Anyone else notice that about 10nm prior to descent in P DES the aircraft accelerates to M0.82 or so from .79 before TOD? In real life it does not do that.
-
Takeoff and descent in PROF mode is recommended actually. You just have to be more aware of what the airplane is doing as opposed to just "setting it and forgetting it". The crew must constantly monitor all phases of flight. As rudimentary as it is, the A300/A310 does better than the EMB-190 in real life. Typical rule of thumb for decent is that youll cross a constraint at the altitude you want, or speed, but not both. In either case, use the spoilers to get you where you need.
-
I have access to an actual APS program for the A300/A310. Side by side they only differ a few degrees. My company limits to 54 I believe but the difference is only a few tenths of percent.
-
Since the latest update the brakes do not release in ALT/ON when the chocks are selected in on the EFB. Once you remove the chocks the appropriate preflight alternate brake check can ben accomplished.
-
Should not be possible unless at least one hydraulic system is pressurized
-
Aircraft schematic and wiring diagram manual.
-
Yes pushing the button will activate the pump for as long as you hold it. Releasing it will cause the pump to shut off 10 seconds after it is released. Like I said previously, this isnt used that often (mostly for the crews during their preflight alt brake check) because the cargo doors do most of the recharging.
-
I could not add this as the topic is locked, however the previous request is wrong. The PB switch in the cockpit is not ON/OFF, it causes the pump to run and then shut off after a 10 second delay. Same system as the cargo doors when the open or close. See below: As you can see in the highlighted section, actuation of that switch or the forward or aft cargo doors causes the yellow electric pump to run. When the cockpit switch or the cargo doors switches are released, the pump runs for 10 seconds until the 36GX relay closes (TDO10S = TIME DELAY OPENING, 10 SECONDS). In the case of either of the 3 switches being activated, the pump running charges the brake accumulator, but actuation of the pump from those switches pressurizes a different part of the yellow HP manifold, therefore most of the yellow hydraulic system is still not pressurized, just the parts to the parking brake accumulator and the cargo doors. The same is for the A300.
-
Can confirm the same here. It takes nearly full deflection of the elevators to achieve liftoff in either standard slat/flaps or 15/15. This is non beta, just latest release of MSFS
-
You’ll have to shut the engines down. It’s normal to not have access after engine start. You can however go to PROG and the FUEL PRED. There you can verify the INIT B values and enter those there.
-
Kind of a silly thing but in the real aircraft opening or closing the forward or aft cargo door (not the bulk) is done through use of the yellow electric hydraulic pump. When actuated it also recharges the brake accumulator. Without charge they typically start bleeding down after about 2-3 hours. Any chance of modeling this?
- 1 reply
-
- 2
-
-
Well when you set up your next fuel load it should properly distribute it so it sort of does.