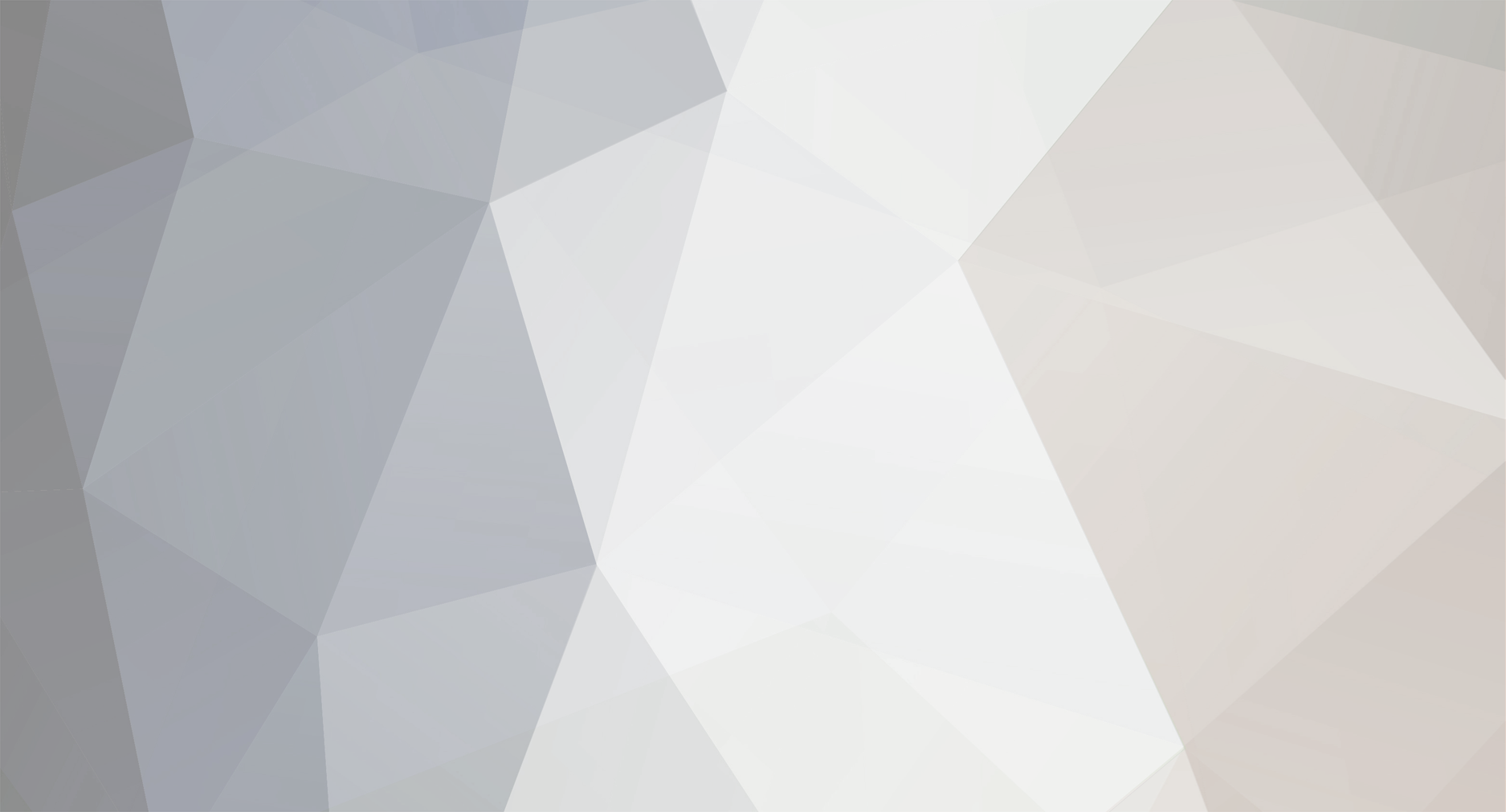
CF104
Member-
Posts
47 -
Joined
-
Last visited
-
Days Won
3
Content Type
Profiles
Forums
Downloads
Everything posted by CF104
-
Sorry to say but you're wasting your time. I've gone through all of this with the initial release for MSFS 2020. INI is totally silent when presented with factual documented evidence. They even reposted the 'how to prevent fuel venting' video for 2024 which is completely wrong for any T-33 ever built. I used to work on the CT-133 (Canadian version) and they don't seem to appreciate input from users with real world experience. There's also a lot wrong with the engine fuel burn and indications. Here's a link to entertain you regarding the fuel system on the MSFS 2020 version. https://forum.inibuilds.com/topic/23761-quick-question-on-the-fuel-system-coding/ Cheers, John
-
Hi Eddie, Thanks for the update. I don't plan on joining another forum to report this. I feel it is incumbent on IniBuilds to report this to WT as you have incorporated their product as part of your package. Regards, John
-
The charts are from a 1962 revision of the RCAF T-33 Mk.3 Aircraft Operating Instruction. I have a 2001 revision but all of the fuel/range performance numbers are in pounds of fuel and not gallons. Yes, the fuel consumption is definitely too high at low power settings and too low at higher settings. This appears to manifest itself in better speed performance at lower power settings along with greater range and less speed performance at high power settings. I was going to post a range performance comparison but all it does is confirm the numbers I posted here and it would probably be much closer once the performance matches these charts. And it's a bit more work as the range charts fuel is in Imperial gallons whereas the sim is in US gallons. Cheers, John
-
Same test but at S.L. All parameters are the same. Very similar trend in performance. Seem that the drag or thrust curves could use some tweaking. Cheers, John
-
Hello, I have just charted out the level speed performance at FL300. The chart indicates over-performance at lower power settings and under-performance at higher power settings. I've attached the Level Speed Performance Chart for the CT-133 and have annotated the results on the chart. It would appear to be either an airframe drag or engine power issue. I' will be charting out another one at a lower altitude to see if there's a correlation. Regards, John
-
Thank you for responding. As someone who takes the time to report bugs, and yes the fuel system is bugged, as well as provide some in depth knowledge and reasoning behind such a report I do find is a bit disingenuous that there is no acknowledgement of the content. A simple thank you for the information and that it's been forwarded to the devs would suffice. I read into the statement "We see it in a stable position at the moment however that does not mean we've abandoned the product.", that INI Builds is stating that the product meets its promises. I highly disagree by quoting the following from your product page. "The in-depth, realistic systems simulations allow you to dive deep into its intricacies, from avionics to engine management.". Both the fuel system and RR engine don't meet the "in-depth and realistic" part of the statement. I've been working on aircraft for 42 years, including the CT-133, and can honestly state that the T-33 is a stupid simple aircraft. It shouldn't be too hard to get it right. I don't mind buying a product in initial release but it feels like this one was rushed. Regards, John
-
Hello, Just wondering if anybody from INI Builds is monitoring this thread? I added some relevant information regarding the T-33 fuel system but it appears this thread is in radio silence. Cheers, John
-
Door warnings are a Level 2 warning and will show the door ECAM page prior to the second engine start. The ECAM priority is a bit of a confusing beast considering the amount of system integration going on. I've attached a simplified diagram that shows the 12 flight phases and the ECAM pages that have priority. Within these flight phases there are multitudes of system inhibits and are too numerous to list here. The logic for the ECAM doors page is covered in flight phase 1 and 12. Any door warning within these phases will bring up the DOOR ECAM page with the following exceptions. The APU start and ENGINE start overlap phase 1 and 2. Engine has the top priority during start and the ECAM will not switch over to the DOOR page at this time. The APU has lower priority over the ENGINE page but will inhibit the DOORS page during APU start until the APU RPM is >95% for 15 seconds or the APU Master Switch is selected OFF. Once the second engine is started the DOOR ECAM page is inhibited. If a Level 2 DOOR warning is indicated via the Master Caution and Aural Warning in any other flight phase, the crew will have to manually select the DOOR ECAM page. In Flight Phase 12 the DOOR ECAM page is back to the priority. Cheers, John
-
Hi, On the G3x with the fuel main page open, go to the Fuel Calc page and then back to the main page. Both the oil pressure and temperature bars lose their color bands. Closing and reopening the fuel page rectifies this. Cheers, John
-
-
Definitely a rag with grit. When I was working on these, the aircrew would have never taken it like this. Cheers, John
-
I'm curious as to the information you have regarding this. IRL, if this were to happen, the jet would be grounded to fix the problem. If this is from a civilian operator of a T-33, then their jet needs some work. Cheers, John
-
No Worries. I just love waking up the old grey matter to remember the CT-133. It's a very simple jet compared to what I have worked on. Cheers, John
-
Sabre drain venting is more of an airframe issue and not the engine. As a fuel user, the engine doesn't have influence over the fuel vent system. Regardless, fuel venting will require taking a lot of things apart to fix. Cheers, John
-
Just adding some technical information as the fuel feed system is NOT working as it does in real life. With no mechanical failures, you can have the tip tanks , LE tanks, Wing tanks and fuse tank pumps all on without venting fuel overboard. There are 3 fuel supply float valves in the fuse tank for each wing group. These float valves are placed at different levels in the fuse tank to provide feed priority to the fuse tank as follows; #1 tip tanks, #2 LE tanks, #3 wing tanks. This means that with all pumps on (gang loaded), the tips feed until empty, then the LE tanks will feed until empty followed by the wing tanks until empty. This all happens automatically due to the float valves and there will not be any venting overboard even with all the pumps on. Gang loading the pumps is not a usual procedure but will NOT result in venting. With the 3 float valves working properly there is no way to overfill the fuselage tank and cause venting. The only way to get fuel venting through the sabre drain is if one or more of the 3 float valves in the fuselage tank has failed, a LE tank or wing tank check valve and boost pump is failed or through unusual attitudes. The information on the way it is currently modelled had to come from somewhere but my experience and training on the CT-133 say otherwise.. Cheers, John
-
Hello, In some lighting conditions the canopy shows a lot of grime and swirls. This isn't very realistic as the swirls look like a sanding disk was taken to the canopy and a dog's been licking it. Screen shot attached. Cheers, John
-
Standard engine issues. Rolls Royce Nene 10 I’ve been doing some flying to test out the Nene 10 as currently modelled. I’ve come across a few issues that differ from the real world Nene 10. Granted it’s been about 30 years since I’ve worked on the CT-133 but these are the things that stand out to me. I’ll begin with the start. OAT @ 15°C, winds calm EGT lags severely during the start. Engine is at idle before EGT is even off the minimum needle indication of 200°C. Digital indicator showing 171°C and climbing. After RPM stable @ 24%, EGT keeps climbing to 586°C after several seconds. The Nene 10 EGT system is quick reacting and has no real perceptible lag in indication. The start acceleration is too fast. On batteries the start takes about 30-35 seconds from starter engagement to 28%. Idle EGT should be in the 430°C to 480°C range and <540°C. Idle Fuel Flow is too high. It is indicating 1600 PPH. This should be 750-800 PPH. Idle RPM in sim is 24% (J33?) whereas the Nene 10 is 28% +/- 1% (this is for CT-133 after mid 60's. Before this the Idle was 20%). Takeoff Power Takeoff Fuel Flow in sim is showing 4000 PPH. This should be 4800-5000 PPH. Takeoff EGT in sim is 511°C whereas the Nene 10 will be @ 650-680°C and <695°C (takeoff max). EGT indicators The modern instrument panel (post AUP) EGT gauge has incorrect markings. The green arc is off scale low and goes to 570°C and the red lines are @ 760°C and 790°C. The green arc should be 200-595°C with 2 individual red lines at 695°C (takeoff) and 800°C (hot start). The classic analogue gauge markings are also incorrect for the Nene 10. In sim the green arc is 250-700°C and the red lines are 700°C and 900°C. The green arc should be 200-595° and the red lines at 695°C (takeoff) and 900°C (hot start). The early CT-133 manuals had the Nene 10 hot start limit @ 900°C but this was reduced in the 70's to 800°C to improve engine reliability. Idle thrust Idle thrust is too high. In sim it will break away and taxi @ 28 knots at idle. The CT-133 will not break away at idle thrust. Standard procedure is to hold the brakes while powering up to 60% rpm, then release them and modulate the power down to maintain taxi speed. Usually somewhere in the 30-35% rpm range depending on fuel weight. The early CT-133 EO's even state that it will need 55% RPM to start rolling. On a level ramp the jet will slowly come to a stop at idle thrust. I’ve included links to some good CT-133 ground run footage which substantiates my observations. Video of CT-133 NENE 10 at idle, RPM 27.7, EGT 431, FF 750 PPH Video of CT-133 NENE 10 at idle, RPM 27.7, EGT 476, FF 750 PPH Video of CT-133 NENE 10 accelerating to TO power Video of CT-133 NENE 10 accelerating from idle to 74% Video of CT-133 breakaway thrust for taxi Video 2 CT-133 breakaway thrust for taxi Video of CT-133 battery start - 30-35 seconds to idle. Cheers, John
-
Hi All, I used to work on the CT-133 about 30 years ago and will provide as good an insight into the Nene 10 operation that I can remember well. One has to realize that the Nene isn't like a modern FADEC engine or even something like a J79 with a full hydromechanical fuel control. The Nene is very simple in terms of engine fuel control. It has 2 fuel pumps with a barometric pressure control and acceleration control unit, a metering valve, a throttle valve and a pressurizing and drain valve. The only thing controlling engine speed is the position of the throttle valve and the overspeed governors in both fuel pumps. The acceleration control unit (ACU) does exactly as it says. During rapid acceleration the ACU will actually reduce fuel pump output to maintain optimum fuel/air ratio to avoid high jet pipe temps and surges during acceleration. The key word is avoid. It will not prevent an idiot from toasting an engine by firewalling it. Given the above info one just can't firewall the throttle and expect the Nene to behave. To avoid over-temp you have to use slow deliberate throttle movements as it doesn't take well to ham-fisted operators. This is a 1940's technology turbine engine and the pilot is part of the engine control equation. Just think of yourself as the engines brain or FADEC. You control the acceleration, deceleration and over-temp control. Cheers, John
-
Regardless whether or not DCS models precession doesn't change the fact that the attitude indicator, in it's current form, is nowhere near how a J-8 is supposed to work and that the one in DCS is a good example of how it functions. That forum post is from someone who used this gauge 57 years ago. I'm sure that the fog of time has blurred some facts and perceptions. If the gauge actually worked as an attitude indicator should then we wouldn't be going down the road of 57 year old memories and probably wouldn't be having this discussion. I'm guessing that INI Builds' intention wasn't to do a study level T-33A with attitude indicator gyro precession etc. If they got it to work according to the documented information I posted, it would be a great plus for this sim. Cheers, John
-
Hi All, Further to my last post regarding the J-8 attitude indicator, I'd like to recommend that if any of the development team has access to DCS that they give the F-86F a try to see its correct behavior. The F-86 has a modified J-8 with pitch lines but it's otherwise the same instrument and operation. Cheers, John
-
The Attitude Indicator, as modeled, is completely wrong in operation. The J-8 Attitude indicator (Mil-I-5133B) is the type installed in the T-33A and is confirmed with the T-33A Parts Catalog T.O.1T-33A-4. The J-8 has gyro stabilized pitch and roll functions. Keep in mind that the T-33 was used as an instrument trainer so having an Attitude Indicator that doesn't actually indicate your attitude is completely useless. The J-8, in it's simplest form, has 3 major visual reference components. The outer components consist of the fixed roll markings and the adjustable pitch trim bar. The gyro stabilized horizon bar indicates roll, and pitch up to 25°(+/-2°) positive and negative. This bar will never go completely out of view as it stops at the 25° pitch limits and will rotate around the periphery of the indicator to maintain the correct down indication of the horizon bar during rolls and loops. The inner sphere has CLIMB and DIVE markings when operating beyond the 25° pitch limits. I've attached screen grabs of the T-33A flight manual that describes the J-8 in very good detail. Cheers, John
-
Well, My seven years of IRL experience on the A300 gives me a different perspective on the matter. I'll dig through our maintenance materials and see if these may differ from your IRL data. Cheers, John
-
Look at the photo the OP posted. The green arc is around the coolest brake (215°C) when it should be around the hottest brake (260°C). Cheers, John (A300 AME)
-
The brake fans on the A306 were an option so there are many A306's out there without them. IRL It's rare to get a brakes hot warning at normal landing weights with autobrakes LO using reverse thrust and disengaging autobrakes at around 60 knots. The jets I work on without fans obviously have warm brakes, <300°C, but rarely do I see a brakes hot warning unless the landing weights were higher than normal or the flight crew tried to make an early high speed exit. We also use the brake fans after arrival to cool the brakes down to be able to carry out our layover cold tire pressure checks sooner. Obviously if you're landing at higher weights/speeds with LO/MED selected you would more than likely get a brakes hot warning. Using MAX WILL give you a brakes hot warning and more than likely melted fuse plugs. In short, you won't get a brakes HOT warning on "every" landing with autobrakes LO selected and using reverse thrust. Cheers, John (A300 AME)
-
Wind will affect the V1 speed along with available runway length. This is due to runway stopping distance. With a headwind the V1 can be higher as your stopping distance required will be less. Conversely with a tailwind your V1 can be less as your stopping distance required will be longer. V1 can never be higher than VR so if the calculated V1 with the tailwind is 157, the VR can never be lower than this. VR will always be greater or equal to V1. V2 can be influenced based on VR although it's basic calculation is thrust, flap setting and weight. Per the A300 flight training manual "VR = Speed at which rotation is initiated to reach V2 at an altitude of 35 feet by the end of the runway." In the headwind example the V1/VR is delayed and therefore the V2 is likely to be higher as the A300 needs to get to the required 35 foot safety altitude while at the same time it's accelerating. In the tailwind example with the lower V1/VR the V2 is lower as well as it will reach the 35 foot safety altitude at a lower airspeed. The one thing you don't see is the absolute V2 number based only on thrust, flaps and weight. One can only surmise from these calculations in your screenshots that V2 is no less than 162 knots. Cheers, John (A300 Mechanic AME)